Mass Timber is shining a light on how to tackle decarbonization
Mass Timber is shining a light on how to tackle decarbonization
Steel and concrete are the dominant structural building materials of our time, but mass timber is proving to be a contender and shines a necessary light on how to tackle decarbonization.
Boston is leading the charge in mass timber with the recent establishment of the Mass Timber Accelerator Program by the Boston Planning & Development Agency (BPDA) and the Boston Society of Architects (BSA). The Accelerator Program included a grant and technical feedback but also the opportunity for Boston area architects, engineers and contractors to develop and share knowledge with one another. DiMella Shaffer’s Project Q was one of seven projects awarded the Accelerator grant in March 2022. Over the span of four months, the process included weekly group meetings with the BPDA and BSA, mid-point and final pin-up presentations, and development of a final report.
DiMella Shaffer’s project is located on a site at Suffolk Downs in East Boston developed by Project Q Communities, OnePoint Partners, and HYM Investment Group. The site includes parcels B018 and B019 and provides 205 units of LGBTQ-friendly senior housing and related amenities. The focus of our study is Parcel B018, a 306,700 square foot building originally designed to be five stories of wood over three stories of steel and concrete podium. To maximize the impact of a lower embodied carbon structural system, the building is instead envisioned with eight stories of mass timber. While steel and concrete are not completely avoidable, their use is limited to the stair and elevator cores, the slab below the second-floor terrace, the first-floor parking/loading dock zone, and slab on grade and foundation walls.
We overcame challenges relating to building form, mixed-uses, and building height. Due to the site’s proximity to the ocean, the building is designed as a rotating concentric C to allow both air flow through the building and sunlight to an elevated terrace. Additionally, the form is driven by the angular site and alignment with the property line. Our study proves that mass timber can be applied to complicated forms and that some rationalization, such as 90-degree angles and exposed mass timber columns at the open terrace, can help to simplify the structure but still maintain the original design intent.
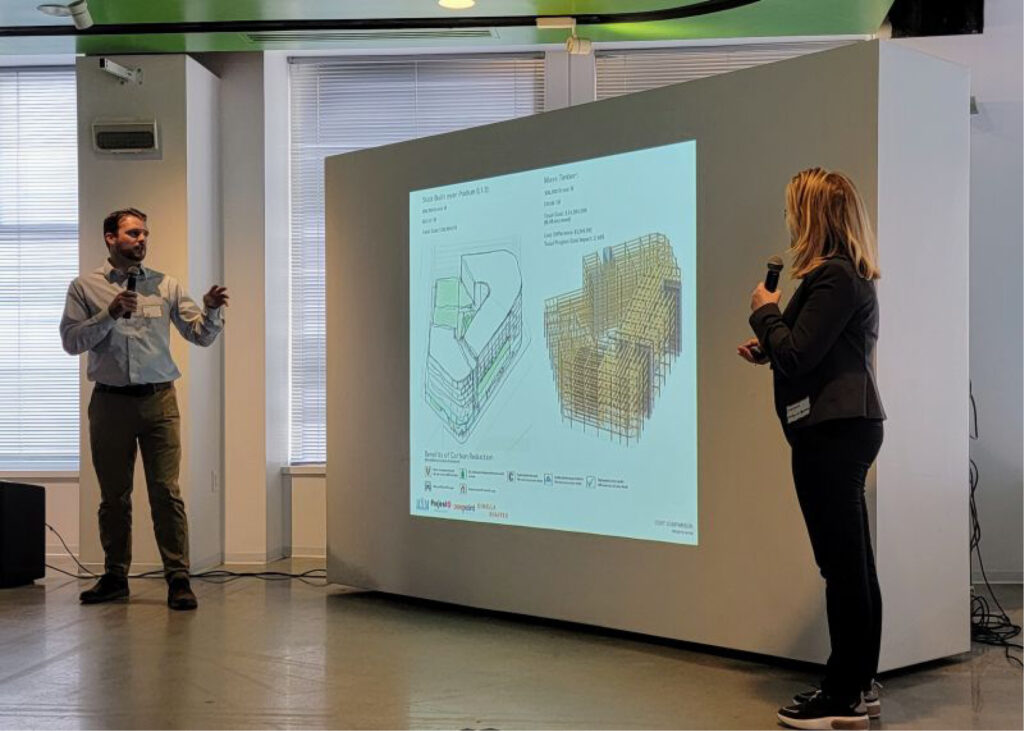
There are various programs within the building: independent living apartments, assisted living units, memory care units, ground floor café/restaurant, fitness, gathering space, and an elevated terrace. Designing a structural bay that works for such a wide variety of programs required careful evaluation. Through collaboration with L.A. Fuess, the structural engineers for the project, typical bay spacing is 25’, 16’, 25’ across the building width, which requires both girders and beams, an obstacle for unit mechanical distribution.
The maximum building height of 85’ is driven by the occupancy use classification and construction type IV-C. We learned that a 10’ floor-to-floor height is possible for the upper independent living units. Without the ability to penetrate the beams and girders, heating, cooling, and ventilation needs to be woven under beams resulting in the lowest height below mechanical distribution to be 6’-9”.
Intuitive tools like Tally and the WoodWorks calculator facilitate carbon analysis and help us to understand our building’s impact on the environment. We thought it necessary to analyze the life cycle analysis of the entire structure including mass timber, steel, and concrete within the Tally plug-in for Revit and calculate the mass timber carbon offset in the WoodWorks calculator. The life cycle analysis of the structure results in a total global warming potential of 1,404,406 kg CO2e and 50 kg CO2e/m2 (4.6 kg CO2e/sf) carbon intensity. Additionally, the 6,770 cubic meters (239,075 cubic feet) of wood calculated for Project Q, could be regrown in just 18 minutes within the US and Canadian forests and equates to 1,764 gas powered vehicles kept off the road for one year.
Without this grant, we may not have had the opportunity to evaluate mass timber to this level of detail and perhaps the discussion may have centered on cost. It was beneficial that we started with many constraints because the challenges pushed us to think creatively. The Mass Timber Accelerator Program created an opportunity for city-wide interaction which is crucial to the advancement of architecture, and to the design of better environments.
You can read our Project Q Mass Timber Accelerator Final Report here.